Comprehensive Battery Test Solution Offerings
It’s common to find advanced battery systems powering a growing range of products, from cell phones, laptops and power tools to electric bicycles and full-scale hybrid electric and plug-in electric vehicles. Emerging cell chemistries provide increasing energy density and expand viable battery applications while at the same time increasing the demand for effective electrical and thermal management of battery pack components. Modern smart batteries include embedded electronics called a Battery Management System (BMS) that serves as the “brain” of the battery pack, optimizing battery performance and ensuring that it operates safely.
DMC designs, builds, and programs automated systems for testing and validation of a broad range of battery pack and battery management system (BMS) designs. Our modular battery management system testing platform incorporates open software and hardware technologies, along with flexible and reliable subsystem components and instruments, to create systems that are completely customizable to the end user’s specifications.
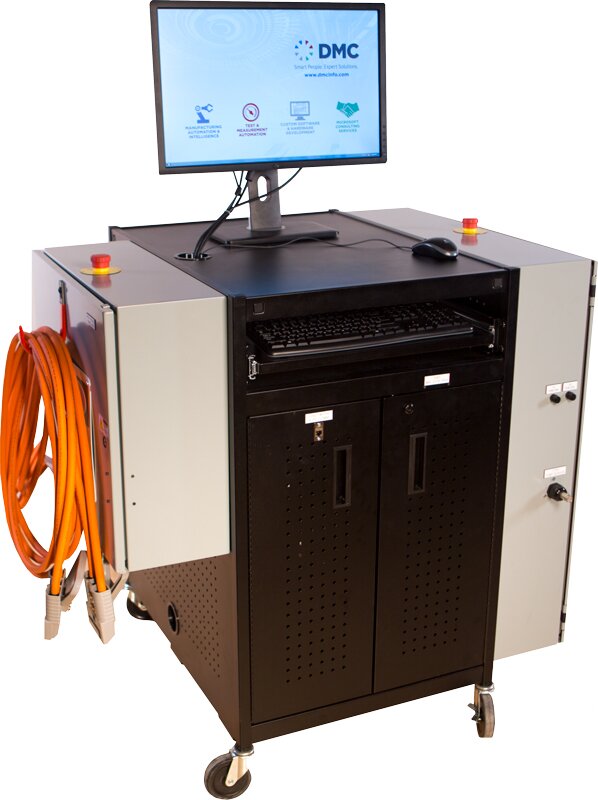
High Power Battery Cycling
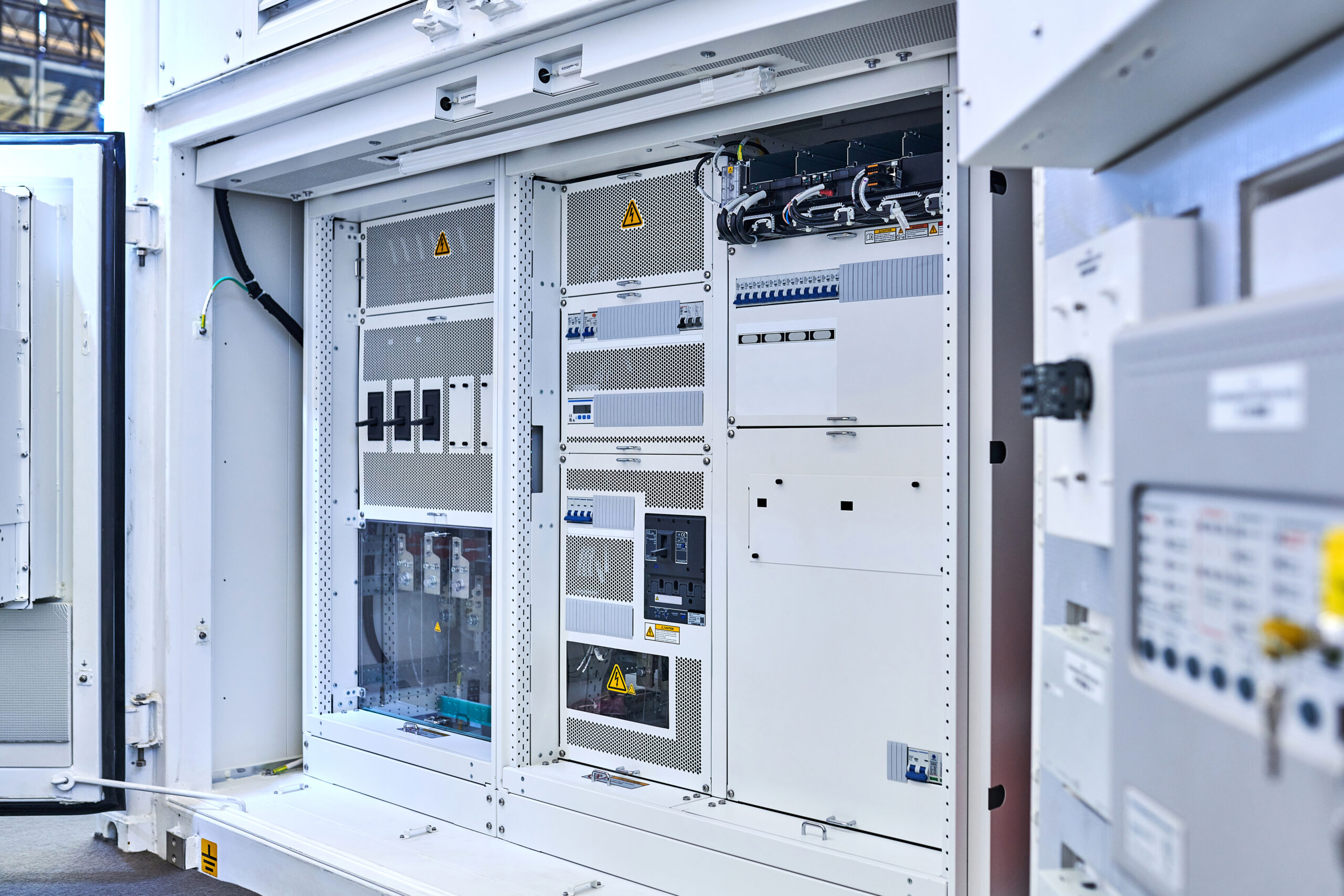
A Battery Pack Test System from DMC can be designed to include battery pack cycling. Our systems can execute standard and customized charge and discharge profiles. Our Battery Pack Test Stands can be integrated into battery cyclers and power supply/DC load platforms from any manufacturer, including:
- Aerovironment Cyclers (AV900, ABC150, ABC170, etc.)
- TDK-Lambda
- NH Research
- Sorensen/Ametek
- Dynapower
Ready to start your next project? We can help.
Battery Pack Test Systems
DMC’s BMS Tests for Battery Packs facilitate battery design as well as research and development for national laboratories and research institutions. They are deployed in end-of-line/production test stations for battery packs developed by major automotive manufacturers and their suppliers.
DMC’s battery pack test systems are designed to evaluate the battery as a complete system and validate a comprehensive range of battery pack functionalities, including:
- Power performance, capacity, DCR / internal resistance
- Contactor and safety interlock functions
- Isolation / insulation resistances
- Reporting of operating data through external communication interfaces (usually CAN)
- Cell voltages
- Pack / cell temperatures
- State of charge (SOC)
- Faults / Diagnostic Trouble Codes (DTCs)
- Electrical characteristics / continuity of internal pack wiring / signals
- Cooling system operation
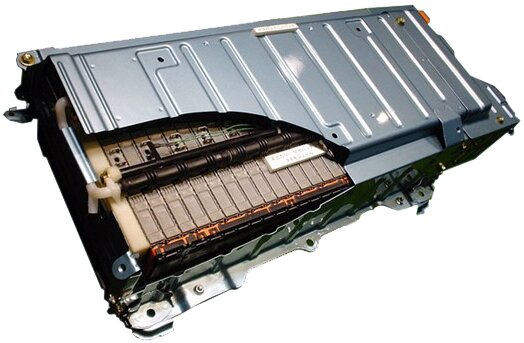
Our test stands are designed to accommodate multiple battery pack testing regimens, including:
Functional Testing
To verify all battery pack communication and data reporting, safety features, wiring, and component functions
High Power Battery Cycling
To evaluate the power characteristics of a battery pack, including charge/discharge behavior, cycle life, and thermal performance
Environmental/Endurance Testing
To test battery pack functions while being exposed to hard/strenuous conditions for extended periods of time
BMS Test Systems
Support for development of various battery types and power modules
DMC’s BMS Test Systems support the development of laptop and consumer electronic batteries, high power lithium ion batteries for electric vehicles, and power modules for a humanoid robotic astronaut on board the International Space Station.
Hardware-in-the-loop approach for BMS testing
For BMS testing regiments, the Battery Management System is tested using a hardware-in-the-loop approach. The test stand itself simulates and controls all inputs to the BMS (cell voltages, temperature sensors, current sensors, CAN data, etc.), providing the ability to subject the BMS to a complete range of possible battery pack states and verify proper BMS responses across operating conditions.
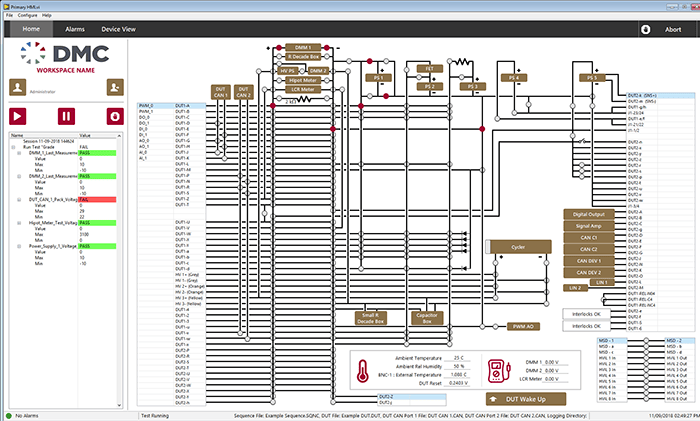
Functionalities evaluated by BMS test systems
DMC’s BMS test systems are designed to evaluate a comprehensive range of BMS functionalities, including:
- Measurement accuracy (cell voltages, temperatures, pack currents, etc.)
- BMS power consumption
- Cell balancing functions
- Reporting of operating data on internal and external communication buses (usually CAN)
- Pack management functions (state of charge calculation, thermal management, etc.)
- Safety functions, contactor control, fault detection, DTC reporting
Testing regiments supported by DMC BMS test stands
DMC’s BMS test stands are engineered to support rigorous validation processes tailored to Battery Management System performance. These systems facilitate both functional testing—ensuring proper communication, fault detection, and system behavior—and environmental testing, which verifies reliable operation under challenging thermal and mechanical conditions. Whether for development, compliance, or durability assessment, our test stands are built to handle a wide range of BMS validation needs.