Paint a Complete Picture with Data Insights
While DCS, SCADA, and PLC systems are limited to collecting data from within their own system, implementing an MES affords the ability to pull data from complex systems across multiple variables to paint a complete picture of the manufacturing environment. The data provided by an MES can help guide and accelerate important business decisions by providing valuable insight into productivity, efficiency, and profitability.
At DMC, we can pull together information from an assortment of sources to provide a centralized place to view all production related information. DMC’s experts have experience working with a wide variety of technologies at the control, SCADA, and MES levels and can leverage that experience to better integrate systems together.
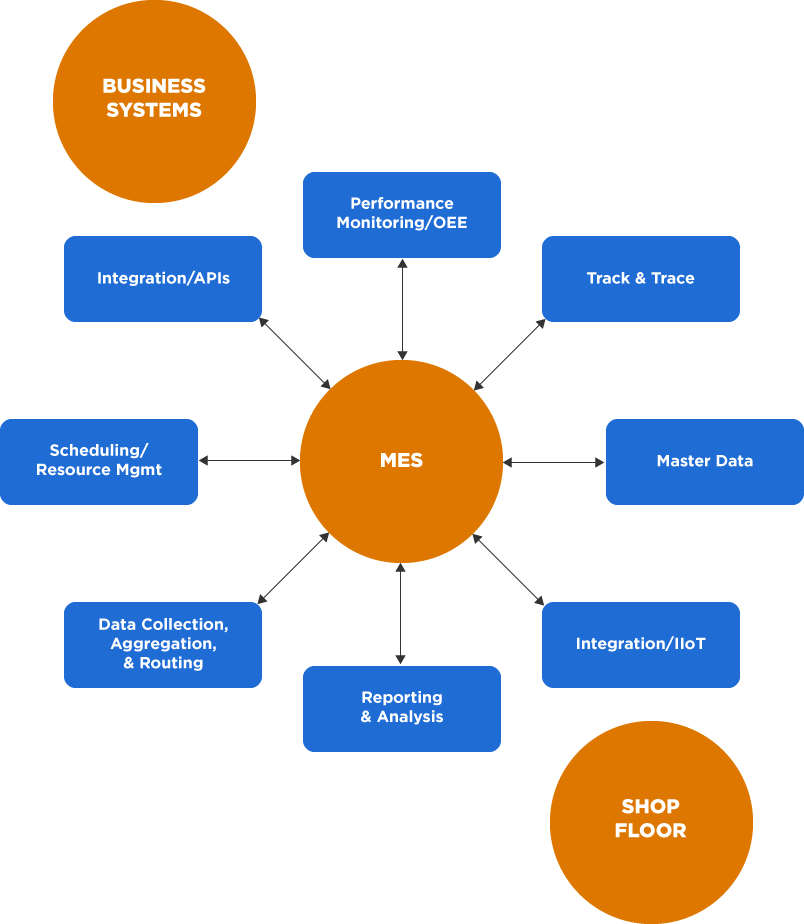
Ready to start your next project? We can help.
On the plant floor, we can aggregate data from existing networked equipment, upgrade existing systems to connect to plant networks, install sensors to collect data from legacy non-networkable equipment, and work with equipment vendors to access data in proprietary systems.
We can also connect to business systems using a range of techniques for legacy and modern deployments. DMC can support both on premise and cloud based data storage and retrieval, and can incorporate IIOT technology, such as MQTT, where applicable.
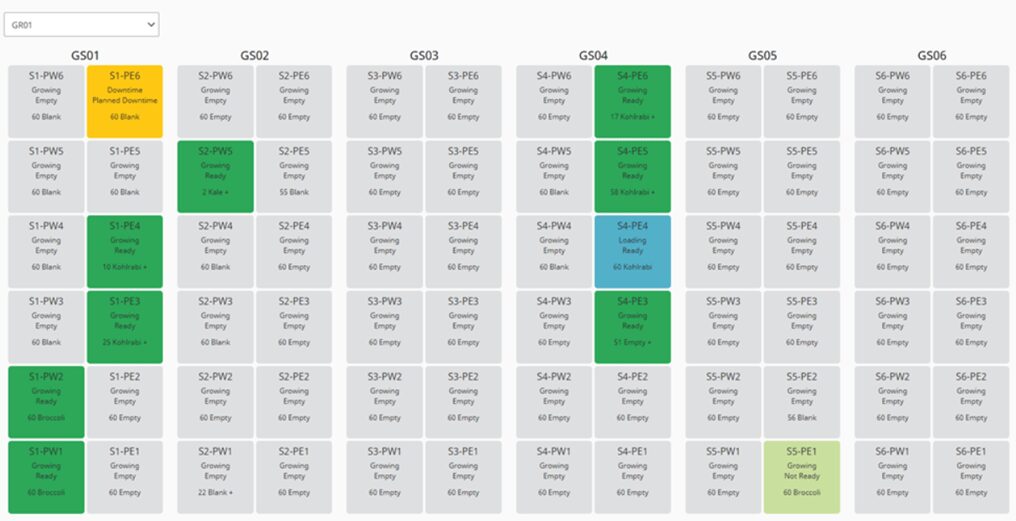
The benefits and applications of deploying an MES for data aggregation include:
- Comprehensive data collection from both manufacturing and business systems
- Dashboards that can visualize data across entire facilities or enterprises
- A centralized hub to share data among many systems without creating duplicate copies of critical data
- Faster troubleshooting with one central place to view data across multiple systems
- Efficient inventory management to balance operation schedule demand with raw materials received
- Traceability and documentation, particularly useful in regulated industries
- A single connection point to integrate new systems into the enterprise
- Centralized automated report generation, including automatically emailed reports
- Integration of shop floor and business systems in one central location
- The ability to predict breakdowns and schedule preventative maintenance to avoid expensive emergency repairs
Identifying patterns, comparing datasets, and tracking developments becomes infinitely easier with visualization, and bolsters knowledge sharing and connectivity by making the information accessible to a much larger audience. Our experienced engineers are able to develop visualization applications for your existing reporting structure, or help you design a new data collection and reporting solution that best fits your project needs.